What is a Sintering Furnace?
Author:Honghai Equipment
Time:2024.12.18
A sintering furnace is a specialized piece of equipment used to consolidate powdered materials into solid forms through the process of sintering. This process involves heating materials below their melting point to enable the bonding of particles through diffusion. Sintering furnaces are essential in a variety of industries, including ceramics, metallurgy, and battery manufacturing, where precision and high-quality materials are critical.
Types of Sintering Furnaces
There are several types of sintering furnaces designed to meet the diverse needs of industries:
- Vacuum Sintering Furnace: Used to prevent oxidation during the sintering process, vacuum sintering furnaces are ideal for materials like metals and ceramics. These furnaces offer a controlled atmosphere that enhances the purity and strength of the final product.
- Hydrogen Sintering Furnace: This type uses hydrogen gas as a reducing agent to eliminate oxides from the material, resulting in improved quality. Hydrogen sintering furnaces are commonly employed in the production of high-purity metal components.
- High-Temperature Sintering Furnace: Capable of reaching extremely high sintering temperatures, these furnaces are ideal for processing materials like zirconia ceramics and refractory metals.
- Continuous Sintering Furnace: Designed for large-scale production, these furnaces provide consistent sintering through a conveyor or belt system, ensuring energy efficiency and high productivity.
- Roller Hearth Kiln: Suitable for continuous production, such as sintering ceramic parts or powder metallurgy components. These kilns use a roller system for high-efficiency, large-scale operations.
- Pusher Furnace: Common in batch production of metal parts or ceramic products, pusher furnaces feature precise temperature control and are used in industries requiring consistent quality.
- Belt Conveyor Furnace (Mesh Belt Furnace): Often utilized for sintering small components in automated systems, these furnaces provide high throughput and consistent processing conditions. The belt conveyor furnace often features a mesh belt, which allows for uniform heating and ventilation. These furnaces are widely used for continuous heat treatment processes like sintering, brazing, and annealing in industries such as powder metallurgy and ceramics.
Applications of Sintering Furnaces
Sintering furnaces are used across a wide range of applications, such as:
- Zirconia Sintering: Zirconia sintering ovens and trays are specifically designed for dental and medical applications, where precision and durability are paramount.
- Battery Materials: Sintering furnaces play a critical role in the preparation of materials for lithium-ion and sodium-ion batteries. They are used to process ceramic powders and create components such as solid-state electrolytes, electrode coatings, and separators. Ceramic powders, including oxides like aluminum oxide (Al₂O₃) and zirconium oxide (ZrO₂), are used to enhance thermal stability and chemical resistance in battery systems. These materials are vital for improving the performance, safety, and lifespan of modern energy storage devices. Additionally, sintering furnaces help achieve the precise temperature control needed to create high-quality cathode and anode materials for both lithium-ion and sodium-ion batteries, driving innovation in the field of energy storage.
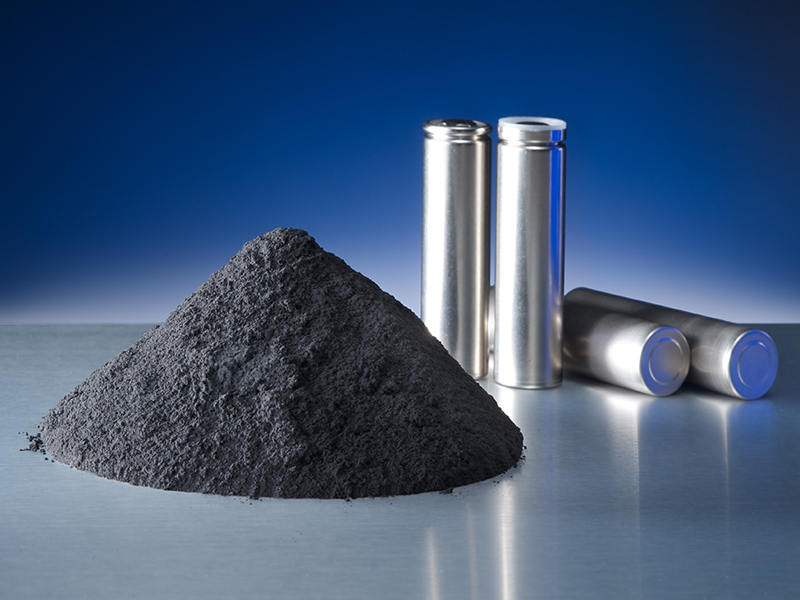
- Industrial Sintering: Sintering processes in industrial applications include the production of components for aerospace, automotive, and electronics.
Key Features of Sintering Furnaces
- Temperature Control: Advanced sintering furnaces come with precise temperature control systems, ensuring optimal conditions for various materials and processes.
- Heating Elements: Modern furnaces use robust heating elements made of materials like molybdenum or graphite, capable of withstanding extreme temperatures.
- Energy Efficiency: Many industrial sintering furnaces are designed to minimize energy consumption, reducing costs and environmental impact.
- High-Quality Outputs: The sintering process ensures that the final products exhibit superior strength, density, and performance.
Sintering Process Explained
The sintering process involves three main stages:
- Heating: The ceramic or metal powder is gradually heated to the sintering temperature, allowing particles to bond.
- Dwell Time: At this stage, the material is held at the desired temperature to allow for diffusion and consolidation.
- Cooling: Controlled cooling ensures that the material retains its structural integrity and desired properties.
Sintering Furnace: A Broad Category or Specific Equipment?
The term sintering furnace can refer to both a general category of industrial furnaces and specific equipment designed for specialized applications. Its definition and scope depend on the context and industry requirements:
1. Sintering Furnace as a Broad Category
Sintering furnaces are often used as an umbrella term for industrial kilns and furnaces that facilitate the sintering process. These can include:
- Roller Hearth Kiln: Suitable for continuous production, such as ceramic or powder metallurgy parts. Its roller system enhances efficiency for large-scale operations.
- Pusher Furnace: Ideal for batch production of metal or ceramic components. The design ensures precise temperature control and consistent output quality.
- Belt Conveyor Furnace (Mesh Belt Furnace): Commonly used in automated systems for small parts, ensuring high throughput and uniform results. The mesh belt design allows for optimal heat transfer and ventilation, making it highly efficient for continuous sintering, brazing, and annealing processes.
- Vacuum Furnace: Employed for high-purity material sintering under controlled atmospheres.
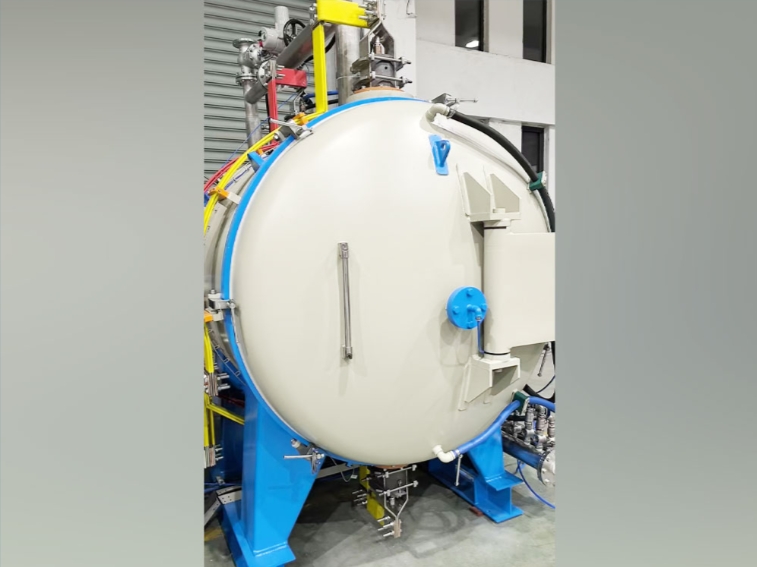
- Hydrogen Furnace: Used to reduce oxides and improve the quality of metallic or ceramic products.
2. Sintering Furnace as Specialized Equipment
In certain contexts, a sintering furnace refers to purpose-built equipment tailored for specific materials or applications, such as:
- Zirconia Sintering Furnace: Designed for precise sintering of zirconia ceramics, commonly used in dental and medical fields.
- Battery Material Sintering Furnace: Specialized for processing lithium-ion and sodium-ion battery materials, emphasizing temperature uniformity and energy efficiency.
- Continuous Sintering Furnace: Optimized for high-volume production of materials like ceramic powders or electronic components.
Understanding these distinctions helps industries choose the right furnace type for their specific needs, ensuring efficiency and high-quality results.
Choosing the Right Sintering Furnace
When selecting a sintering furnace, consider the following factors:
- Material Requirements: Whether you are working with ceramic powder, metals, or battery materials, the furnace should match the specific sintering needs.
- Temperature Range: Ensure the furnace can achieve the required sintering temperature for your materials.
- Energy Efficiency: Opt for a furnace with low energy consumption to reduce operational costs.
- Manufacturer Reliability: Choose sintering furnace manufacturers with a reputation for producing high-quality, durable, and efficient equipment.
Advancements in Sintering Technology
Modern sintering furnaces incorporate innovations such as:
- Improved Energy Efficiency: Reducing energy consumption without compromising performance.
- Automation: Continuous sintering furnaces with automated controls enhance productivity and precision.
- Customizable Features: Tailored solutions for specific applications, including advanced zirconia sintering trays for dental and medical uses.
Conclusion
A sintering furnace is an indispensable tool in industries requiring the precise consolidation of powdered materials. From hydrogen and vacuum sintering furnaces to high-temperature and continuous models, these machines cater to various industrial applications. As demand for high-quality, energy-efficient solutions grows, sintering furnace manufacturers continue to innovate, ensuring that the sintering process remains a cornerstone of advanced manufacturing technologies.